Six Sigma Black Belt Training Course
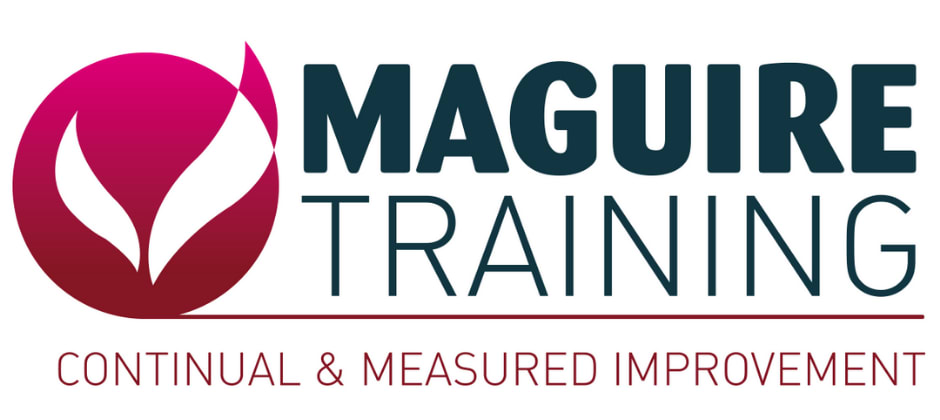
At the end of Lean & Six Sigma Black Belt training you will have a far greater knowledge of how the 2 methodologies can improve & enhance the business.The training will involve 10 days of classroom training and practical work.
This is then followed by 2 on the job projects, which involves using all the tools correctly and making a cost saving or increase in productivity that would enhance the company profit by a minimum of £100,000 each project. Alternatively, you can complete one project to the value of £100,000 within 6 months and prove a history of 3 years in a role of quality management and should have worked in process improvement projects.
During the project stage the trainer will meet with each delegate once per month. During these sessions they will check they are on track with their project (in terms of using the right tools, passing each stage and making savings), ideally this is a face to face session. We can mix some remote sessions with face to face sessions if need be.The at the end of the project(s) they need to meet again to validate that they have used the correct “tools”, made the right savings and be certified as Six Sigma Black Belts.
Upcoming start dates
Suitability - Who should attend?
This top-tier programme is ideal for those professionals who are already experienced in applying the Six Sigma Methodology as the lead on complex projects as a full-time Project Manager leading teams that include both yellow and green belt practitioners. The Lean Black Belt Six Sigma training course will guide you through all aspects of Lean Six Sigma methodology to an advanced level of competence.
Outcome / Qualification etc.
Learning Outcomes
- Apply the black belt six sigma tools and methodologies to projects
- Undertake every stage of a project to black beltstandards
- Showan in-depth knowledge of applying the black belt six sigma DMAIC
- Implement defined solutions
- Apply operational change management techniques within their defined scope
- Lead large scale black belt improvement projects
- Mentor yellow and green belts
- Identify areas within their business where six sigma black belt projects can be applied.
- Lead and improvement team
Training Course Content
Part 1: Define Phase
Six Sigma Basics
- Meanings of Six Sigma
- Deliverables of aLean Six SigmaProject
- The Problem-Solving Strategy Y = f(x)
- Voice of the Customer, Business and Employee
- Six Sigma Roles & Responsibilities
- Defining a Process
- Serious Quality Characteristics (CTQ’s)
- Poor Quality Cost
- The Pareto Analysis (80:20 rule)
- Six Sigma - Measurement Standards
- Building a Business Case & Project Charter
- Developing Project Metrics
- Financial Evaluation & Benefits Capture
- The Combination of Lean & Six Sigma
- The Seven Waste Elements
Part 2: Measure Phase
Process Definition- Cause & Effect / Fishbone Diagrams
- Process Mapping, SIPOC, Value Stream Map
- X-Y Diagram
- Failure Modes & Effects Analysis (FMEA)
- Basic Statistics
- Descriptive Statistics
- Normal Distributions & Normality
- Graphical Analysis
- Precision & Accuracy
- Bias, Linearity & Stability
- Gage Repeatability & Reproducibility
- Variable & Attribute MSA
- Capability Analysis
- Concept of Stability
- Attribute & Discrete Capability
- Monitoring Techniques
Part 3: Analyse Phase
Patterns of Variation- Multi-Variation Analysis
- Classes of Distributions
- Understanding Inference
- Sampling Techniques & Uses
- Central Limit Theorem
- General Concepts & Goals of Hypothesis Testing
- Significance; Practical vs. Statistical
- Risk; Alpha & Beta
- Types of Hypothesis Test
- 1 & 2 sample t-tests
- 1 sample variance
- One Way ANOVA
- Mann-Whitney
- Kruskal-Wallis
- Mood’s Median
- Friedman
- 1 Sample Sign
- 1 Sample Wilcoxon
- One and Two Sample Proportion
- Chi-Squared (Contingency Tables)
Part 4: Improve Phase
Simple Linear Regression- Correlation
- Regression Equations
- Residuals Analysis
- Non- Linear Regression
- Multiple Linear Regression
- Confidence & Prediction Intervals
- Residuals Analysis
- Data Transformation, Box-Cox
- Experiment Objectives
- Experimental Methods
- Experiment Design Considerations
- 2k Full Factorial Designs
- Linear & Quadratic Mathematical Models
- Balanced & Orthogonal Designs
- Fit, Diagnose Model and Center Points
- Designs
- Confounding Effects
- Experimental Resolution
Part 5: Control Phase
Lean Controls- Control Methods for 5S
- Kanban
- Poka-Yoke (Mistake Proofing)
- Data Collection for SPC
- I-MR Chart
- Xbar-R Chart
- U Chart
- P Chart
- NP Chart
- Xbar-S Chart
- CumSum Chart
- EWMA Chart
- Control Methods
- Control Chart Anatomy
- Subgroups, Impact of Variation, Frequency of Sampling
- Center Line & Control Limit Calculations
- Cost Benefit Analysis
- Elements of the Control Plan
- Elements of the Response Plan
Request information - obligation free
For over two decades, Maguire Training has been providing businesses and individuals all over the world with industry-leading leadership, management, sales and personal development training for real, tangible results. Maguire Training is an endorsed training provider of the Institute of...